Abu Dhabi, 2013: This follows my previous article on Pottery Making workshop experience. I was delighted to see the pieces had survived the drying process. Those who love colours, you can imagine how delighted I was in being informed that the moment of choosing the colours and the glazing had arrived.
Aah, but first, a bit of sanding and buffing is required before applying the wax and then the glaze.
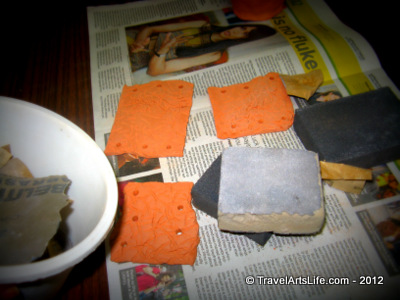
It’s Buffing up time. You can choose sand papers of different grit sizes to buff the rough edges, but best advice is to go gentle.
Aaah, but first, one must finish applying the wax at the bottom of the pieces. This is so that the glazes once they melt will not dribble onto the bottom of the kiln and kill the kiln.
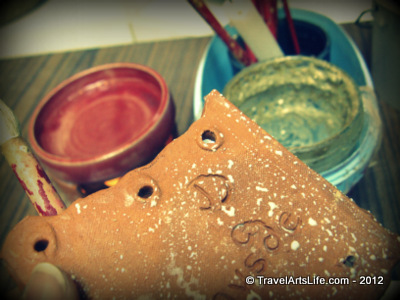
The wax is applied to the bottom of the slabs and also whereever we don’t wish for the glaze to touch.
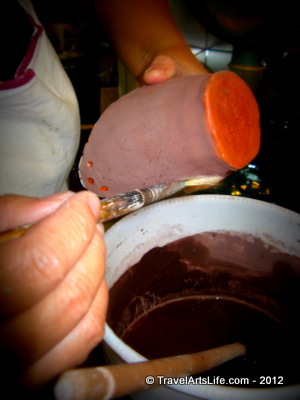
Mary assists me in cleaning some of the ‘glaze’ dust where ever it is too thick otherwise it may melt away to the bottom of the kiln and ruin it
Visit Abu Dhabi Pottery. Part III is when we finally unveil the glazed pieces and our creative hands finishing the pieces with a bit of crochet wire and 16 gauge wire.
[…] gently (I use the integrative arts as my favourite thawing tool, whether that be dance movements, attending handcraft workshops, poetry therapy, blog story therapy, creating intuitive art, creating videos, designing cufflinks […]